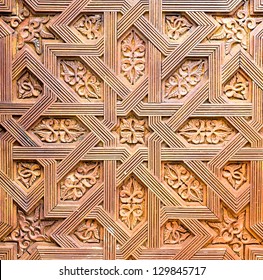
Wood carving tools with sharp edges will enhance your enjoyment. These are the most common ways to sharpen your wood carving tool. Sharper edges last longer and are more durable than dull ones. Sharp edges allow for more efficient use of your tools. Sharp edges make carving easier and ensure maximum cutting performance. Listed below are three common methods of sharpening wood carving tools. Read on to learn more. - Using a Sharpening Stone.
Sharp edges are a great way to enhance your carving experience
In addition to sharp tools, the best carving experience is achieved by using tools with razor-sharp edges. Sharp tools require less effort and provide more control during carving. Also, a blade that has been sharply cut leaves a smooth surface. A successful carving project requires sharp tools. For optimum results, hone your carving tools regularly. Regular sharpening will keep them sharp and make your carving work much easier.
While sharp edges may increase the satisfaction of carving, they may cause blisters in the process. Wood's texture is natural and will not be smoothened with regular handling. Calhouns will develop from the blisters. However, this is a slow and painful process. If you notice blisters in your carving, try to change the way you hold your tools. It will take practice, but it is worth it.
Start by sharpening your knives with a sharpening tool and a fine-grained rock. You must also inspect for damage at the edges. Chips in the edge area will require more aggressive grinding. A dull edge may only require minimal grinding on a finer grit stone. Test the knife by cutting through paper or rope. You may not need to sharpen the knife if it has been dull for some time.
Common techniques for sharpening wooden carving tools
There are many different methods of sharpening wood carving tools. There are several ways to sharpen wood carvings tools. Oil stones require oil to be applied on the stone's surface to prevent metal particles from embedding themselves in the surface. Diamond and ceramic stones are oil-free and can be used to sharpen carbide wood carving tools. This article will talk about the common methods of sharpening wooden carving tools.
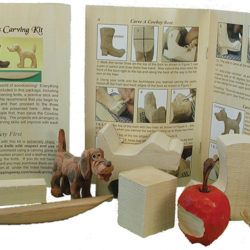
The leather strop is used to remove the wire from a blade's edge and polish it. Although a leather strop works well for most tools, some carvers prefer to use a textured one. A flat leather strop is best for straight tools, or the outside edge gouges. A leather strop with grooves is for those who are serious about their work.
Traditional bench chisels were sharpened at a 25 degree angle and a secondary bevel of five degrees. Modern alloys can't be used with these angles and may break. To correct this, raise the angle of bevel. This requires more force but will allow you to control the bevel better. Block planes are sharpened at a twenty-degree angle.
A sharpening iron is required
To sharpen wood carving tools, you can use a sharpening stone. The stone is made up of grit which is a crystalline mineral that is much harder than steel. It also has sharp edges. The stone will require a lubricant to aid in cutting and prevent metal particles getting stuck. Once you have sharpened your edge to make it easier to cut wood, it will also be less resistant. The strop is usually made from leather and serves to remove burr and polish the edge.
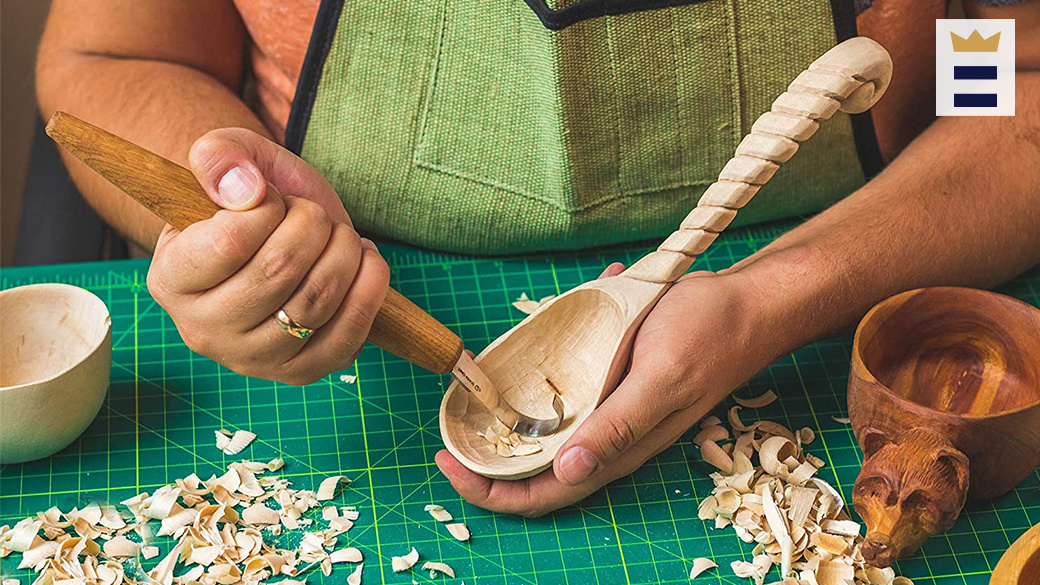
There are many types and brands of sharpening tools on the market. You can choose from oilstones, waterstones or ceramic stones. The oil stones use oil as a lubricant to avoid fine metal particles from burying themselves in the stone surface. The lubricants that are needed for ceramic and diamond stones are not required. They are both effective in sharpening carbide wood carving tools.
Sentima is an excellent example of a high-quality sharpening system. It features a coarse and fine stone, both made of corundum. This material features a consistent grain that allows for fast cutting and smooth finishes. Its unique design is easy to clean. The sharpening device is made from durable materials that will not deteriorate over time.
FAQ
Are there any other things I should know regarding woodworking?
Furniture making is a laborious task. It's easy not to appreciate how hard it is. Finding the right type of wood is the most difficult aspect of this process. There are so many options for wood, it can be difficult choosing the right one.
Another problem is the fact that not all wood has the same properties. Some woods will warp and others will split or crack. These factors should be taken into account before buying wood.
How long does it take to finish a piece of furniture?
It depends on the wood type you choose, the complexity and the amount you apply to the finished product. Hardwoods are more difficult to maintain than softwoods. Hardwoods also tend to be more expensive than softwoods. But they last longer, and resist moisture better. It takes between one and three months to finish a piece.
What is the difference between a hobbyist woodworker and a professional woodworker.
Hobbyists enjoy making things out of wood, whereas professionals focus more on the quality of their work. Hobbyists often take pride in the creations they make and often share them to family and friends. Professionals will spend hours looking at designs before they start to build a project. They will meticulously plan every detail of their work from choosing the right materials to finishing it.
How do I organize my shop?
Setting aside an area to store tools is the first step in keeping your workshop organized. You want your tools to stay clean and free from debris and dust. Pegboard hooks can be used to hang tools and accessories.
What kind of wood should you use?
The most popular types of wood used in woodworking include oak, pine, birch, maple, cherry, mahogany, teak, poplar, redwood, and bamboo. Each wood type has its own characteristics which affect the final product's appearance and feel. For example, oak tends to be darker and harder than other woods. Birch is lightweight and soft while mahogany is heavier and denser. You can also pick between veneers and solid wood. Veneers are thin sheets of wood that are glued together to form a single layer.
Statistics
- If your lumber isn't as dry as you would like when you purchase it (over 22% in Glen Huey's opinion…probably over 10-15% in my opinion), then it's a good idea to let it acclimate to your workshop for a couple of weeks. (woodandshop.com)
- The U.S. Bureau of Labor Statistics (BLS) estimates that the number of jobs for woodworkers will decline by 4% between 2019 and 2029. (indeed.com)
- The best-paid 10 percent make $76,000, while the lowest-paid 10 percent make $34,000. (zippia.com)
- Most woodworkers agree that lumber moisture needs to be under 10% for building furniture. (woodandshop.com)
External Links
How To
How to stain hardwood
Staining wood is the process of applying chemicals to the wood's exterior, which alters its color. This chemical reaction changes the wood's color from white to brownish. Oak is the most commonly used wood for staining, but other woods can also be stained.
There are many ways to stain wood surfaces. You can mix the stain with a solvent, such as turpentine, and spray it onto the wood. You can also apply a solution containing water and dye directly to the wooden surface. You can also mix stains with varnishes or paints so that they become part the finish coating.
Preparing your wood for staining is the first thing to do. To apply the stain, clean the wood completely. Sanding the wood removes scratches and imperfections. The next step is to choose the stain type you want. There are two main types of stain: non-penetrating and penetrating. Penetrating stains penetrate deeper than non-penetrating stains, which makes them great for dark colors like mahogany. The best non-penetrating colors are those that work with light colors like maple.
You will need to decide on the type of stain you want to use, and then prepare your tools. You can use a paintbrush to apply stains. This allows you spread the liquid evenly over the surface. You should also have some handy rags to wipe up excess stains after you finish painting. You should have enough containers to store the various components of the stain mixture if you intend to mix it yourself.
After you have prepared the materials, you can clean the area where you want to stain the wood. Use warm water and soap to clean away dirt and dust. Use a dampened rag and clean water to wipe the furniture. Be sure to get rid of all loose material, especially if staining is planned for darker wood.
Apply the stain next. The stain can be applied by spraying or brushing the stain onto one end of the furniture. Slowly and carefully work your way along the grain to reach the opposite end. Keep the stain from dripping off the wood's surface. Allow the stain to dry completely before you move on to the next step.
Apply a clear polyurethane sealant to protect the painted surface. Apply three coats polyurethane sealer. Allow the third coat to dry overnight, before sanding.