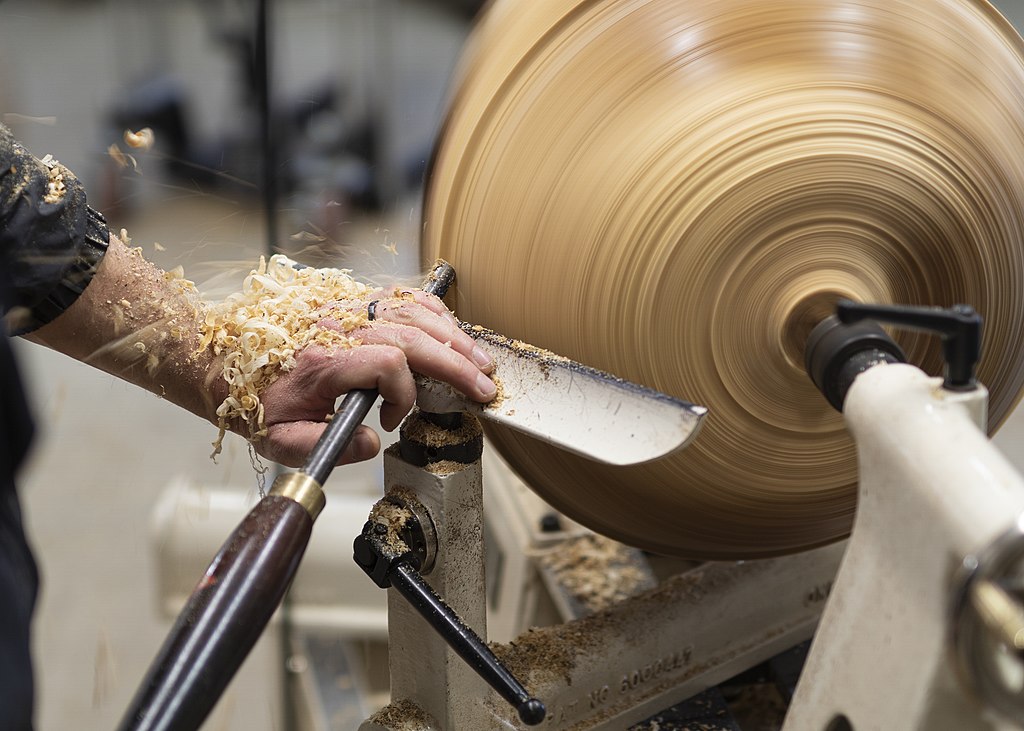
There are many types dovetail tools. Dovetail lathes are typically made with an included angle at 90 degrees. Figure 3 shows two 0.100"-dia. Dovetail tools come in different sizes and include angles. They are suitable for many applications and can be purchased in different sizes. This article will discuss the differences and compare the two types.
Dovetail milling cutter
Dovetails refer to pieces of wood that have been arranged parallel on a lathe. Also known as jigs, dovetails can also be called jigs. They can be used for manufacturing but not for automotive. Dovetails are among the most commonly used woodworking tools. The dovetail is not just a tool for woodworking. It can also be used in optical systems.
A dovetail cutting cutter is a type or chamfering device that can be used to create reliefs, bevels, and other features on the undersides of stock. This tool can also be used as a deburring tool to flatten aluminum. These tools are often micro-grain carbide and come in a variety of lengths, geometries, and cutting diameters.
You can pair dovetail lathes with vices to hold small workpieces. These vices can be placed on a table at an angle up to 90 degrees for machining. You can also make dovetails in an opposite direction. The first must be cut parallel with the first and the second at 90 degrees to the first.
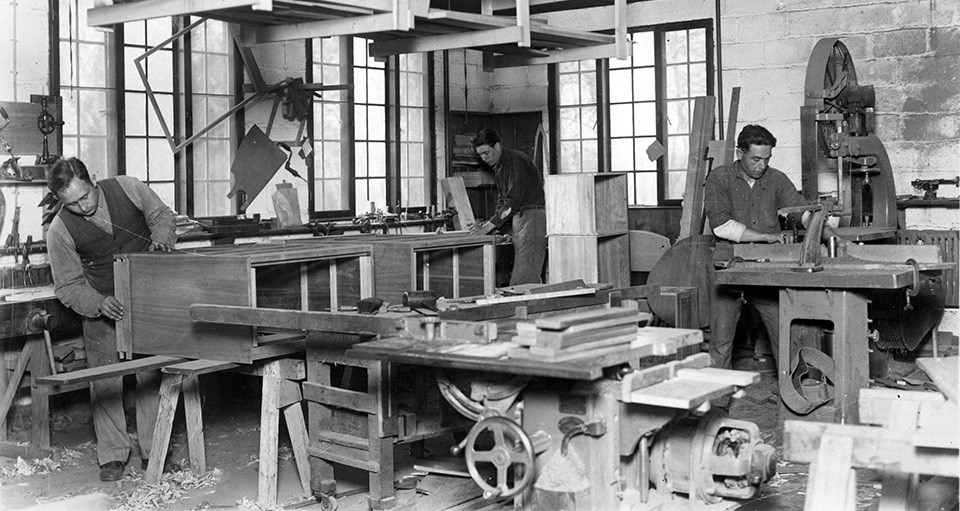
Many dovetail lathe tools can be too big for their dovetails. This causes imperfections in surfaces and can sometimes lead to tool failure. Dovetail cutters, on the other hand, are designed to be smaller than the standard end mill, with a smaller neck diameter. In other words, dovetail lathe tools should be chosen with care, and the tool should be selected appropriately.
Dovetail chisel
A dovetail saw will help you make the job much easier. A good dovetail saw will allow you to get a better angle for cutting dovetail tailboards. Ashley Iles' dovetail chisel is a great choice. It has a triangular cross section, and plenty of flexibility for easy use. These chisels are also available with an oiled cloth on the base of the pocket.
A good dovetail tool will allow you to create a dovetail recess fast and efficiently. It features a triangular blade cross section that can be used to fit into tight corners of a dovetail. Its hollow back provides maximum holding power. A handy mark-out scale is included with the chisel to help you determine the right diameter for your dovetail.
An umekinomi is another dovetail chisel. This Japanese traditional chisel can remove waste from dovetails. The tool has a triangular crosssection and narrow edges. Its blades are made of a combination hard high-carbon Hitachi steel on the front and soft steel at the back. Takao Shubano, a Japanese master blacksmith, makes the blades. This tool has more than 50 years' experience in toolmaking.
Nova Dovetail Chisel
A quality dovetail tool is essential to get the best out of your dovetail machine. Nova Dovetail Chisel is used to cut the dovetail recess in your dovetail jaws. The dovetail-chuck chuck will be able to hold it well because of its unique shape. The other chisels are not designed with the same dedicated shape, which can lead to poor dovetail form and improper seating of the jaws. It comes with a handy measuring scale that measures the diameter of your dovetail recess. You can make dovetails with it for either 50mm (2") or 100mm (4") jawsets.
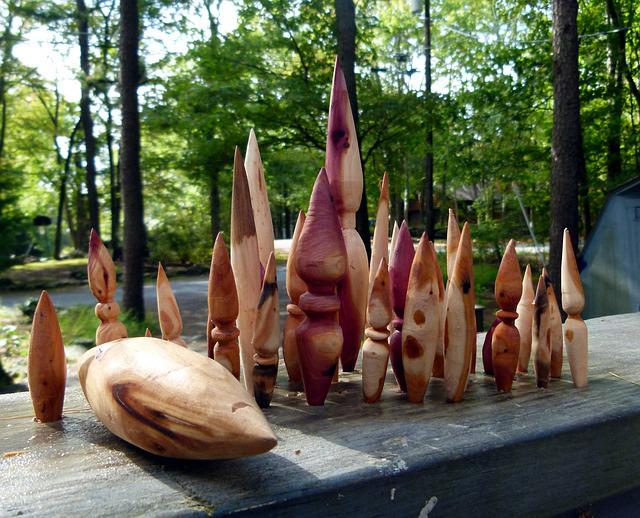
The NOVA Dovetail Chuck Accessory makes it possible to create a dovetail groove for your dovetail chucking. The NOVA Accessory Jaws match perfectly, ensuring a precise cut with a comfortable grip. The NOVA Dovetail Chisel, made by Teknatool International, comes with a 2-year replacement warranty.
Nova Dovetail Chisel's ease of use is another benefit. It does not require the Turner to maintain a bevel edge, which is the most challenging part of dovetail lathe work. The design makes it easy to use for both beginners and professionals. The Nova Dovetail Chisel's sharpening is simple.
FAQ
Is it possible to open my own woodworking shop?
It is not easy to start a woodworking business. There are many laws and regulations you need to be aware of. However, it doesn't necessarily mean you must go through all the hassle of setting up a business. Many people choose to join existing businesses. You will only have to pay membership fees, taxes, and other charges.
What is the difference between a hobbyist woodworker and a professional woodworker.
Hobbyists love making things from wood while professionals are more concerned with the quality of their work. Hobbyists usually take pride in their creations and often share them with friends and family. Before they start working on a project, professionals will spend hours researching the designs. Professionals will be meticulous about all aspects of their work, from selecting the right materials to finishing it.
How do you know which tools are the best for you?
It's important to consider your preferences and needs when buying tools. Do you prefer metal handles or plastic? What size of nails and screws do your hands use most? Do you prefer to use hand tools or power tools?
How much should a woodworker charge per hour?
The hourly rate paid to a professional woodworker is dependent on many factors. These include skill level, availability, and location.
The average hourly rate for a skilled woodworker ranges from $20-$50 an hour.
An hourly rate of $10 for a less skilled woodworker could be possible.
Where can I purchase woodworking supplies
There are many places you can get everything you need, and you don't have to go far. You could also visit hardware stores in your area or shop online at Amazon.com.
You can also check garage sales and flea markets for old furniture and other materials you can reuse.
Where can I start woodworking?
Building furniture is the best way to learn how furniture is made. Although you will need to have tools and may make mistakes along your journey, you'll soon be able to master it.
Choose a project that interests you. You can make a simple box or a large entertainment center. Once you've settled on a project find a local skilled woodworker. Ask your local woodworker to help you determine the right tools for you and where they are located. Maybe you can ask the person if they know of anyone who does this sort of work.
How do I calculate woodworking prices
It is essential to calculate costs as accurately as possible when pricing any project. Make sure you're getting the best prices on materials. You should also consider other factors that could impact the cost of your project, such as experience, skill level, time, and money. If you want to get an idea of what you can expect to spend on different types of woodwork projects, check out our guide to the average price of common household DIY tasks.
Statistics
- The best-paid 10 percent make $76,000, while the lowest-paid 10 percent make $34,000. (zippia.com)
- In 2014, there were just over 237,000 jobs for all woodworkers, with other wood product manufacturing employing 23 percent; wood kitchen cabinets and countertop manufacturing employing 21 percent. (theartcareerproject.com)
- Overall employment of woodworkers is projected to grow 8 percent from 2020 to 2030, about as fast as the average for all occupations. (bls.gov)
- Average lumber prices rose about 600 percent between April 2020 and May 2021. (familyhandyman.com)
External Links
How To
How to make wooden joints
This tutorial will show how to join 2 pieces of wood together. We will use the pocket hole joint, which is drilling holes in the wood to join them. This works well if the wood is straight and smooth. If your wood isn't straight or flat, you might want to try another method, such as dowel joinery. These are the steps
-
Drill Pocket Hole Joints. Measure and mark the location where you would like to place the pocket hole joint. You will then drill 3/4" deep holes through each piece of wood with a jigsaw, handheld drilling machine, or hand-held drill.
-
Sand Smooth. You can sand the edges of the wood to ensure that it doesn't split.
-
Glue Together Apply glue on both sides of the wooden plank. Let the wood sit for 5 minutes, then clamp it together.
-
Attach the Pieces together. After the glue has dried completely, you can clamp the pieces together until they are flush.
-
Trim Joinery. After the glue dries completely, trim off any excess wood around the joint.
You should leave enough space between the pieces to allow you to turn them inside-out.